THE CHALLENGE
An operator of one of Canada’s largest airports, ensures, among other responsibilities, that every building on the airport site is appropriately heated.
Using a vast boiler system to heat expansive areas, it is crucial that they follow strict boiler code to monitor water levels to avoid overheating, which can create risk of explosion and adversely affect all airport operations and safety.
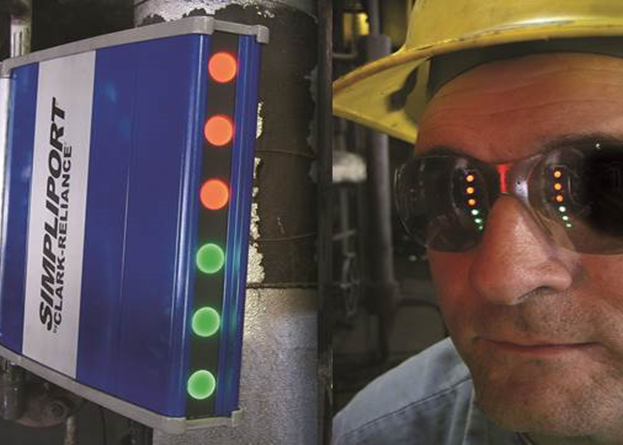
THE NEED
Adhering to the boiler code, our client required level measurements to be completed with at least one direct reading gauge, which must be kept in continuous service.
While everything was to code with their gauges, they were using glass level gauges to monitor the boiled water used to generate heat in buildings. This created possible challenges as the glass gauges were prone to breaking and difficult to read unless the operators were within close proximity to the gauges, creating potential safety risks.
THE WAJAX SOLUTION
Although there was not an immediate need to replace the glass gauges as per code and standard industry practice, Wajax evaluated the opportunity to upgrade the system while addressing the safety challenges. Part of the solution Wajax proposed included implementing Simpliport® 180 gauges.
These gauges allowed for reliable direct-reading with their digital bi-color indication of water levels. In addition, operators would be able to clearly see the gauge within 180° regardless of where they stood. The gauge displayed a bright red or green indication of steam and water levels so that the operators could quickly and clearly see if action needs to be taken.
THE IMPACT
Operators no longer need to be on the ground or within close proximity to monitor levels. Instead, they can now view the gauges from a control room 50ft away.
This distance monitoring increased personnel safety by reducing the need for operators to be in the boiler environment. It also reduced the need for intervention as a result of the breakage of the glass level gauges.
The outcome of the evolved system helped reduce downtime and the risk of a shutdown in the event of overheating that would cost hundreds of thousands of dollars to repair in damages.
With increased safety and decreased maintenance needs, these gauges met the criteria for the boiler code while providing the most effective outcome for the customer.
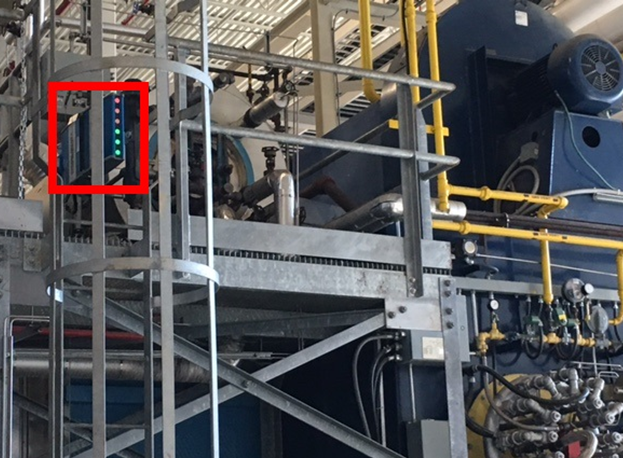